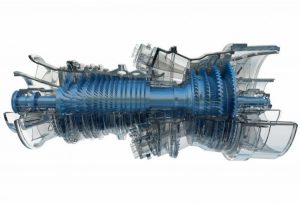
آشنایی با پره های توربین گازی
1- مقدمه
توربینهای گازی در صنایع نفت و گاز به طور عمده در زمینههای پمپ و انتقال نفت و گاز و همچنین تأمین برق کاربرد دارند. وجود ۶۵۰ دستگاه توربین گازی با بیش از ۳۶ مدل در صنایع نفت و گاز ایران تاکنون (سال ۱۳۸۳) و پیشبینی افزایش تعداد آنها در سالهای آتی از یک طرف و ارزبری بالا و محدودیتهای موجود در تأمین قطعات به ویژه پرههای توربین گازی از بازارهای خارجی از طرف دیگر، لزوم تأمین قطعات توربینهای گازی از بازارهای داخلی و حمایت از تولیدکنندگان داخلی را بیش از پیش میطلبید. جدول 1، انواع و تعداد توربینهای گازی موجود در صنایع نفت و گاز ایران را نشان میدهد.
تضمین کیفیت پرههای توربین گازی به لحاظ حساسیت و استراتژیک بودن آنها برای مصرفکنندگان و همچنین پیچیدگی این قطعات به لحاظ شرایط کاری خاص آنها، تولید این قطعات را مستلزم دستیابی به سطح بالایی از دانش فنی و تکنولوژی مینماید که خوشبختانه این پتانسیل در داخل کشور وجود دارد. امید است با اعتقاد راسخ به خودباوری و توانمندیهای مهندسین و متخصصین داخلی و تجهیزات و امکانات موجود در کشور بتوان در راستای خودکفایی گامهای مؤثری را برداشت.
۲– توربین گازی
توربینهای گازی زمینی جهت تبدیل انرژی سوخت به شکلهای دیگری از انرژی اعم از الکتریکی یا مکانیکی طراحی و ساخته میشوند. یک توربین گازی اصولاً متشکل از یک بخش ژنراتور گازی و یک بخش تبدیل قدرت میباشد. بخش ژنراتور گازی شامل کمپرسور، محفظه احتراق و توربین میباشد. در یک توربین گازی، هوا توسط قسمت کمپرسور از اتمسفر مکیده میشود. کمپرسور دارای ردیفهای متناوبی از پرههای متحرک و ثابت میباشد که عملکرد آنها باعث فشرده شدن هوای ورودی میشود.
بخشی از هوای فشرده وارد محفظه احتراق شده با سوخت مخلوط میگردد. احتراق حاصل از سوخت و هوای فشرده منجر به تولید گازهایی با دماهای بالا میگردد که وارد قسمت توربین میشود. توربین نیز شامل چند ردیف از پرههای ثابت و متحرک میباشد. گازهای داغ حین ورود به قسمت توربین به پرههای ثابت که به شکل نازل میباشند برخورد میکنند. در این حالت فشار گازها کاهش یافته و سرعت آنها افزایش مییابد. سپس گازهای داغ به پرههای متحرک برخورد نموده و در اثر برخورد با ایرفویل پرهها، سبب چرخش مجموعه پره، دیسک و شفت میگردند. بخشی از کار تولیدشده در توربین جهت چرخش کمپرسور به کار میرود و باقیمانده آن به تجهیزات از توربین منتقل میشود.
در انتهای قسمت توربین، ردیفهای اضافی از پرهها وجود دارد که فشار گازها توسط آنها به حالت اولیه در موقع ورود به کمپرسور برمیگردد. این ردیفهای اضافی از پرهها در صورت مجزا بودن از ردیفهای اولیه توربین، خود یک توربین مجزا در نظر گرفته میشوند که تحت عنوان توربین قدرت (Power Turbine) معروف هستند. در توربینهای گازی با یک چنین طراحی به آن بخش از توربین که بلافاصله بعد از محفظه احتراق قرار گرفته توربین کمپرسور (Compressor Turbine) اطلاق میشود.
توربینهای گازی با توان بالا که عمدتاً به منظور تولید برق طراحی شدهاند و اصطلاحاً به آنها Generator Drive گفته میشود دارای بخش توربین قدرت نمیباشند. اما توربینهای گازی که به منظور انتقال نفت و گاز طراحی شدهاند و به آنها Mechanical Driveگفته میشود شامل بخش توربین قدرت میباشند. در صنایع نفت و گاز ایران از هر دو گروه توربین گازی مذکور وجود دارد. به عنوان نمونه، توربین گازی مدل MS 6001B برای تولید برق، توربین گازی مدل Type S7 و TA1750 برای انتقال نفت و مدل EM 85 برای انتقال گاز موند استفاده قرار گرفتهاند. شکل ۱ نمونهای از توربین گازی نوع Mechanical Drive را که در مناطق جنوب ایران در زمینه انتقال نفت مورد بهرهبرداری قرار دارد را نشان میدهد. این مدل از توربین گازی دارای بخش توربین قدرت میباشد.
۳– پرههای توربین گازی
یک توربین گازی در قسمتهای کمپرسور و توربین (توربین کمپرسور یا توربین قدرت) دارای یک یا چند ردیف از پرههای ثابت و متحرک میباشد. پرههای ثابت و متحرک در توربینهای گازی مختلف دارای طراحیهای مختلفی میباشند.
با توجه به اینکه پرههای قسمت توربین به لحاظ شرایط کاری نسبت به پرههای قسمت کمپرسور بیشتر دچار تخریب میشوند و سهم عمدهای از تقاضای بازار برای پرههای قسمت توربین میباشد مطالب ارائهشده عمدتاً مربوط به این پرهها میباشد.
3-1- پرههای ثابت
پرههای ثابت وظیفه سرعت دهی به گازهای ورودی به توربین را دارند. محصولات احتراق که دارای فشار بالایی میباشند.
در مسیر ایجادشده توسط پرههای ثابت، در ترت فارء افزایش سرعت پیدا کرده و همچنین جهت مناسب برای برخورد به پرههای متحرک را پیدا میکنند.
شرایط کاری پرههای ثابت به گونهای است که در معرض تنشهای گریز از مرکز نمیباشند ولی به دلیل آنکه گازهای ورودی به توربین دارای دما و فشار بالایی هستند امکان از بین رفتن سریع این پرهها به ویژه پرههای ردیف اول در اثر خسارتهای ناشی از اکسیداسیون و خوردگی، خزش، خستگی سیکل پایین و سایر موارد وجود دارد.
پرههای ثابت با توجه به شرایط کاری در توربینهای مختلف و همچنین ردیفهای مختلف یک توربین دارای جنس و طراحی متنوعی میباشند. پرههای ثابت در شکلهای مختلف به صورت تکی و یا سگمنت ۲ با چندتایی طراحی و ساخته میشوند. معمولاً پرههای ثابت ردیفهای جلویی جهت محافظت و خنککاری دارای پوشش و یا کانال و سوراخهای هوا میباشند. شکلهای 2 و 3 طراحیهای تصحیحی مختلفی از پرههای ثابت در توربینهای مدل EMBS و مدل Centaur را نشان میدهد. همچنین تصاویری از انواع پرههای ثابت تولیدشده (مهندسی معکوس) در شرکت موادکاران در انتهای کتابچه ارائه شده است.
3-2- پرههای متحرک
پرههای متحرک توربین با تبدیل انرژی درونی گازهای ورودی به انرژی مکانیکی موجب چرخش روتور و به دنبال آن کمپرسور میشوند.
پرههای متحرک نیز مانند پرههای ثابت به دلیل تماس با گازهای با دما و فشار بالا در معرض انواع خرابیها میباشند. پرههای متحرک علاوه بر اینکه تحت تنشهای ناشی از برخورد گازهای داغ به سطح ایرفویل قرار دارند در معرض تنشهای گریز از مرکز شدید به واسطه سرعت درونی بالای محور توربین (چندین هزار دور در دقیقه) نیز میباشند و بنابراین تنشهای وارد بر پرههای متحرک بیشتر از تنشهای وارد بر پرههای ثابت میباشد.
پرههای متحرک در مدلهای مختلف توربین گازی و همچنین در ردیفهای مختلف یک نوع مدل توربین به دلیل شرایط کاری مختلف دارای جنس و طراحیهای متنوعی میباشند. اکثر پرههای متحرک از ۳ قسمت اصلی ایرفویل (Air Foil) شنگ (Shank) و ریشه (Root) تشکیل میشوند.. برخی از پرههای توربین علاوه بر این موارد دارای قسمت شرود (Shroud) نیز میباشند. شکلهای ۳ و ۴ نمونههایی از پرههای متحرک توربین گازی بدون شرود و دارای شرود را نشان میدهند. در شکل ۴ قسمتهای مختلف پره متحرک نشان شده است. همچنین تصاویری از انواع پرههای متحرک تولید شده (مهندسی معکوس) در شرکت موادکاران در انتهای کتابچه ارائه شده است.
4- مواد ساخت پرههای توربین
پرههای قسمت توربین (توربین کمپرسور و توربین قدنت) به دلیل کار در درجه حرارت بالا و محیط خورنده و اعمال شوکهای حرارتی، تنشهای خستگی (در ریشه پرههای متحرک)، تنشهای ضربهای (ناشی از برخورد ذرات خارجی) و سایر تنشها دارای شرایط کاری بسیار سخت بوده و در معرض انواع خرابیها قرار دارند. بر این اساس، ساخت پرههای توربین نیازمند بکار گیری مواد ساخت مناسب، طراحی مناسب (طراحی کانال و سوراخهای هوا جهت خنک کاری پرهها / یا استفاده از پوشش) و همچنین بهکارگیری امکانات تجهیزات و روشهای ساخت و تولید ویژهای میباشد. با توجه به شرایط کاری این پرهها، معیارهایی که در انتخاب مواد آنها مطرح میباشد عبارتاند از:
- مقاومت به خزش
- مقاومت به خستگی
- مقاومت به اکسیداسیون
- مقاومت به خوردگی
- مقاومت به سایش
- مقاومت به ضربه
- قابلیت ریختهگری
- قابلیت جوشکاری
سوپر آلیاژها به دلیل دارا بودن خواص سازگار با شرایط کاری و تولید پرهها سالهاست که به عنوان مواد ساخت پرههای توربین شناخته شدهاند و همچنان به موازات پیشرفت در طراحی و ساخت توربینهای جدید، تحقیقات در زمینه توسعه سوپر آلیاژها نیز ادامه دارد.
سوپر آلیاژها قابلیت کار در دما و تنش مکانیکی بالا و در محیطهای خورنده را داشته و عموماً بر پایه یکی از عناصر نیکل، کبالت و آهن میباشند. سوپر آلیاژهای پایه نیکل به دلیل داشتن ترکیب بهینهای از خواص مورد اشاره در بالا نسبت به ۲ گروه دیگر از اهمیت بیشتری برخوردارند. جدول ۲ جنس پرههای قسمت توربین (توربین کمپرسور و توربین قدرت) انواع توربینهای گازی مورد استفاده در صنایع نفت و گاز ایران را نشان میدهد.
همانطور که در جدول ۲ مشاهده میشود اکثر پرهها از جنس سوپر آلیاژ میباشند. ترکیب شیمیایی و خواص مکانیکی این سوپر آلیاژها در انتهای کتابچه ارائه شده است.
۵- مراحل تدوین دانش فنی و ساخت پره
5-1- شناسایی پره
در این مرحله با استناد به مدارک و یا پرهای فابریک شناسایی متالوژیکی و مکانیکی پره صورت میپذیرد. در شاخه شناسایی متالوژیکی موارد جنس، نوع پوشش، خواص مکانیکی، متالوگرافی و میزان عیوب داخلی پره مورد ارزیابی قرار گرفته و با مقایسه نتایج آزمایشهای انجامشده بر روی پره فابریک و استانداردها و مدارک معتبر سازندگان، شناسنامه این پره اقتباس میگردد، این شناسنامه در ادامه تولید در کنترل کیفی پرههای تولید شده مورد استناد قرار میگیرد. همچنین در مرحله شناسایی مکانیکی پره، نقشههای دقیقی از ایرفویل و شنگ پره توسط CMM و ریشه پره توسط Profile Projector تهیه شده و پره میانه برای ساخت قالب فلزی انتخاب میگردد، تلرانسهای ابعادی ایرفویل و ریشه پره با توجه به استانداردهای کنترل ابعادی موجود و اندازهگیری پرههای فابریک اقتباس شده و نقشه کامل شده فابریک تهیه میگردد.
– تهیه شمش سوپر آلیاژ
سوپر آلیاژهای مورد نیاز از سازندگان معتبر خارجی خریداری میگردد.
5-3- طراحی و ساخت قالب فلزی
این مرحله یکی از اساسیترین مراحل ساخت پره میباشد زیرا که تأمینکننده ابعاد نهایی پره که از دقتهای بسیار بالایی برخوردار میباشد است. همانگونه که در قسمت شناسایی پره اشاره شد نقشه دقیق استخراج شده از پره، مبنای ساخت قالب فلزی قرار میگیرد ولی میبایست درصد انقباض موم و فلز در این قالب در نظر گرفته شود. با توجه به اینکه ممکن است مبردهای مومی قبل از تزریق در داخل قالب فلزی قرار بگیرد محاسبه میزان انقباض نواحی مختلف مدل مومی از فعالیتهای بسیار پیچیده میباشد. جهت تأیید و در خط تولید قرار گرفتن قالب فلزی، اولین قطعات ریختهگری شده از این قالبها و خود قالب فلزی توسط CMM اندازهگیری و ارزیابی میشوند.
5-4- طراحی و ساخت گیجهای کنترل ابعادی
گیجهای کنترل ابعادی مختلفی در مراحل ساخت پره مورد استفاده قرار میگیرد. بعد از مرحله شناسایی مکانیکی پره و تهیه نقشههای کامل پره این فعالیت شروع شده و با توجه به شکل و اندازه پره معمولاً سه سری گیج کنترل ابعادی مهیا میگردد:
الف- گیجهای کنترل ابعادی موم
ب- گیجهای کنترل ابعادی پره ریختگی
ج- گیجهای کنترل ابعادی ریشه و قسمتهای ماشینکاری شده گیجهای کنترل موم و پره ریختگی مجهز به ساعتهای اندازهگیری با دقت صدم میلیمتر گیجهای کنترل ابعادی ریشه در حد میکرون میباشد.
۵-۵- طراحی سیستم راهگاهی
بهمنظور حصول بهترین شیب انجمادی و ساختار کریستالی داخلی و دانهبندی سطحی، سیستم راهگاهی پره طراحی شده و خوشههای مومی و سپس سرامیکی تهیه میگردد، بعد از ذوب ریزی، طرح مواد مورد ارزیابی خواص متالوژیکی و مکانیکی قرار گرفته و در صورت لزوم تغییراتی در آن اعمال میگردد.
5-6- تهیه قالبهای سرامیکی
قالب فلزی تزریق موم در این مرحله بکار گرفته شده و پره مومی تهیه میگردد. پرههای مومی از خارج شدن از قالب در صورت لزوم در قالبهای نگهدارنده موم قرار گرفته تا کاملاً بهصورت کنترل شده سرد شوند. مومها سپس توسط گیجهای کنترل ابعادی خاصی کنترل شده و مومهایی که از نظر ابعادی مورد تأیید قرار میگیرند در سیستم راهگاهی مونتاژ شده و خوشه مومی تشکیل شده در خط دوغابدهی سرامیکی قرار میگیرد. بعد از نشاندن حدود ۱۰ لایه سرامیک بر روی این خوشهها، آنها را در دستگاه اتوکلاو قرار داده تا موم آنها تخلیه گردد. سپس خوشههای سرامیکی در دمای بالاتر از پخت میشوند تا استحکام لازم جهت ریختهگری را کسب نمایند.
۵-7- ریختهگری پره
ریختهگری پرهها به روش ریختهگری دقیق در خلأ صورت میپذیرد. به این منظور از کوره VIM (Vacuum Induction Melting) استفاده شده و قالبهای سرامیکی قبل از ریختهگری پیشگرم میشوند. هر دوی مراحل پیش گرم و ریختهگری، در خلأ انجام میگردد. طی چند مرحله ریختهگری آزمایشی و ارزیابی خواص متالوژیکی و مکانیکی و ابعادی پرهها شرایط دمای ذوب ریزی، دمای گرم، سرعت بارریزی و نحوه سرد کردن پره بعد از ذوب ریزی تعیین شده و تثبیت میگردد. به منظور کنترل ابعادی پره ریختگی از گیجهای ساعتی ساختهشده استفاده شده و ابعاد پره ریختگی با توجه به شناسنامه موم همان پره مورد ارزیابی قرار میگیرد. همچنین آزمایشهای FPI، رادیوگرافی، دانهبندی، متالوگرافی، کشش و خزش پرههای ریختهگری شده به منظور ارزیابی شرایط ریختهگری در این مرحله صورت میپذیرد.
۵-8- کنترل کیفی
بعد از تثبیت شرایط ریختهگری، پرهها دریچهای مشخص ریختهگری میشوند و آزمایشهای کنترل کیفی آنها صورت میپذیرد تا پرههای تأییدشده به مراحل بعدی تولید ارسال شوند، آزمایشهای کنترل کیفی به دو گروه تقسیم میشوند آزمایشهای غیر مخرب و آزمایشهای مخرب.
آزمایشهای غیر مخرب بر روی تمامی پرهها صورت میپذیرد و شامل آزمایشهای بازدید چشمی، FPI، رادیوگرافی، دانهبندی سطحی و کنترل ابعادی میباشد. آزمایشهای مخرب نیز شامل کشش، خزش، آنالیز شیمیایی و متالوگرافی هستند. نمونههای استاندارد آزمایشهای کشش و خزش از داخل پرهها و یا به صورت AS Cast تهیه شده و در دمای محیط و دماهای بالا (تا ) مورد آزمایش قرار میگیرند. همچنین یک پره از یک بچ ریختگی به طور کامل تخریب شده و در نواحی مختلف ایرفویل و ریشه توسط میکروسکوپ و دستگاه آنالیز تصویر، عیوب انقباضی و ناخالصیهای آن مورد بررسی قرار میگیرند.
آنالیز شیمیایی نمونهای از هر بچ ریختگی نیز توسط دستگاه کوانتومتر یا XRF و دستگاههای دقیق دیگر اندازهگیری میشود. در تمامی موارد آزمایشهای غیر مخرب و مخرب، معیارهای کنترل کیفی از استانداردهای معتبر جهانی در مورد پرههای توربین و سوپر آلیاژهای مورد نظر اقتباس میشود. کنترل ابعادی پره توسط گیجهای ساعتی و گیلیون گیج صورت میپذیرد. این گیجها توسط پره فابریک مبنا کالیبره میشوند و تلرانسهای ابعادی مورد قبول از پرههای فابریک و استانداردهای کارخانههای سازنده پره اقتباس میشود.
5-9- انجام عملیات فشار داغ (HIP)
پرههای تأییدشده در کنترل کیفی جهت بالا بردن ضریب اطمینان و کاهش پراکندگی خواص و نهایتاً افزایش طول عمر، جهت عملیات HIP به خارج از کشور ارسال میشوند.
5-10- ایجاد کانالهای خنککننده
برخی از پرهها به دلیل کارکرد در شرایط کاری دمای بالا، نیاز به کانالهای خنککننده دارند که از دو روش ماهیچه گذاری و STEM استفاده میگردد. در روش STEM کانالهای خنککننده پره توسط دستگاه STEM ایجاد میگردند. و در روش ماهیچه گذاری نیز از ماهیچههای سرامیکی که بعضاً در داخل محلولهای شیمیایی خاصی حل میگردند استفاده میگردد. سطوح این کانالها دارای زبری خاصی است که بازدهی خنککنندگی پرهها را افزایش میدهد. دستگاه STEM در ایران موجود نمیباشد و پرهها جهت سوراخکاری مستقیماً بعد از عملیات HIP در خارج کشور به محل کارخانه مورد نظر جهت سوراخکاری ارسال میشوند. فعالیتهای تبادل اطلاعات فنی، ساخت فیکسچرها و سوراخکاری پرههای آزمایشی تا به دست آوردن پارامترهای ماشینکاری توسط شرکت سفارشدهنده پیگیری میگردد و به محض حصول نتیجه مطلوب، سوراخکاری پرههای هرست انجام میگیرد.
5-11- ماشینکاری
ریشه پرههای توربین گازی از دقت ابعادی بسیار بالایی برخوردار هستند و کلاس دقت آنها در حد میکرون است. با توجه به سختی و چقرمگی سوپر آلیاژ، ماشینکاری ریشه پره از روشهای معمول امکانپذیر نیست و معمولاً در تمام دنیا از دستگاه سنگزنی خزشی استفاده میشود.
به منظور سنگزنی خزشی لازم است پره در فیکسچرهای بسیار صلب قرار گیرد تا در اثر نیروهای بالای سنگزنی هیچگونه ارتعاشی در پره صورت نپذیرد. در روش سنگزنی خزشی در هر پاس میتوان چند میلیمتر باربرداری انجام داد و سنگ نیز به طور پیوسته توسط تیزکن تیز میگردد تا تلرانس ابعادی قطعه حفظ شود. بعد از سنگزنی، ابعاد پره توسط گیجهای کنترل ابعادی شامل پین گیجها، گیج بروو نرو و گیج توازی سطوح و کیفیت سطوح آن توسط FPI مورد ارزیابی قرار میگیرد.
مراحل سنگزنی شامل سنگزنی کاج ریشه، بغلها و سرپره میباشد.
5-12- پوششدهی
قسمت ایرفویل بعضی از پرهها توسط پوششهای PVD با نفوذی از نوع RT22 پوشش دهی میشوند. امکانات داخلی و خارجی برای انجام این فرآیندها موجود میباشد.
5-13- عملیات حرارتی
به منظور بهینه کردن ساختار متالوژیکی پره، عملیات حرارتی حل سازی جزئی و پیرسازی بر روی پرهها صورت میپذیرد. این عملیات در کورههای تحت خلأ و یا در اتمسفر با گاز محافظ انجام میشود.
5-14- شات پین
به منظور حذف اثرات مضر سنگزنی خزشی، ریشه پرهها بعد از عملیات حرارتی شات پین میشوند. این عملیات نیز توسط دستگاه خاص صورت میپذیرد. این دستگاه توسط چندین نازل ساچمههایی با سایز مشخص را با فشار و زاویه مشخص بر روی سطوح ماشینکاری شده میباشد تا با ایجاد تنش فشاری سطحی، عمر خستگی ریشه را افزایش دهد.
5-15- ردیفچینی و بستهبندی
در آخرین مرحله، پرهها بالانس وزنی شده و توسط برنامه کامپیوتری ردیفچینی میشوند و همراه مدارک کنترل کیفی در بستهبندی مناسب تحویل کارفرما خواهند شد.
برای دریافت فایل مقاله روی آشنایی با پره های توربین گازی کلیک کنید.
5 دیدگاه برای “آشنایی با پره های توربین گازی”
سلام
آیا همه قطعات داخل توربین دارای کوتینگ میباشد؟ در صورت ورود حجم زیاد اسید، چه اتفاقی برای قسمتهای مختلف توربین گازی می افتد و عواقب آن چیست؟
سلام وقت بخیر. با واحد مهندسی شرکت تماس بگیرید.
سلام وقت بخیر
span کجای پره محسوب می شود؟
سپاس
با سلام و احترام
جسارتا میتونم از مطالب این بخش از سایت در بخشی از سمینار خودم با ذکر منبع استفاده بکنم؟
سلام. باذکر منبع اشکالی ندارد. امیدواریم مفید باشد.